“Good product – good idea” – Das ist das Motto des Vorzeige-Werkes der Marke Lexus von Toyota (über eine Million Besucher seit Start of production 1992). Hier werden die Modelle RX, CT, NS und HS hergestellt.
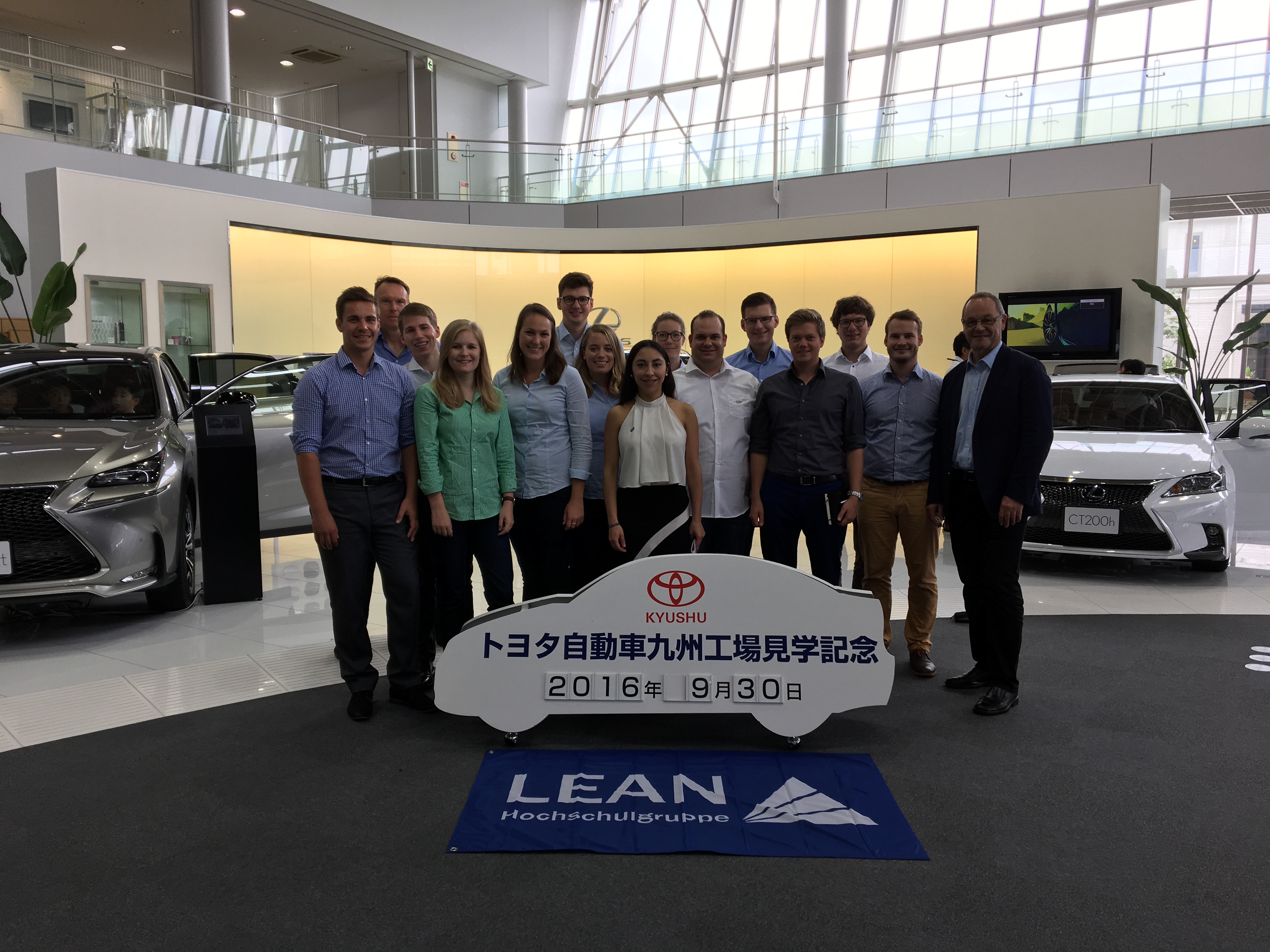
🌐 TOYOTA Motor Kyushu,Ltd (トヨタ自動車九州株式会社 宮田工場)
In dem 1 km² großen Werk werden von 9300 Mitarbeitern 430.000 Fahrzeuge pro Jahr produziert.
Die Mitarbeiter arbeiten im Zweischichtsystem von ( 6:00 – 14:45 / 16:00 – 00:45 ). Hierbei ist die Taktzeit pro Auto variabel und wird monatlich an die Auftragslage angepasst. Die Durchlaufzeit eines Autos von Presswerk bis zum Ende der Montage beträgt 19 Stunden. Möglich wird dies unter anderem dadurch, dass es keinen Puffer zwischen Lackiererei und Endmontage gibt. Im Miyata Plant stellt Toyota Fahrzeuge her, die zu 90% für den ausländischen Markt bestimmt sind.
Nachdem wir uns einen ersten Eindruck über die Produkte geschaffen haben, sind wir per Bus an die Montagelinie gefahren und haben unsere Besichtigung gestartet. Dabei haben wir als Gruppe die folgenden Eindrücke gesammelt:
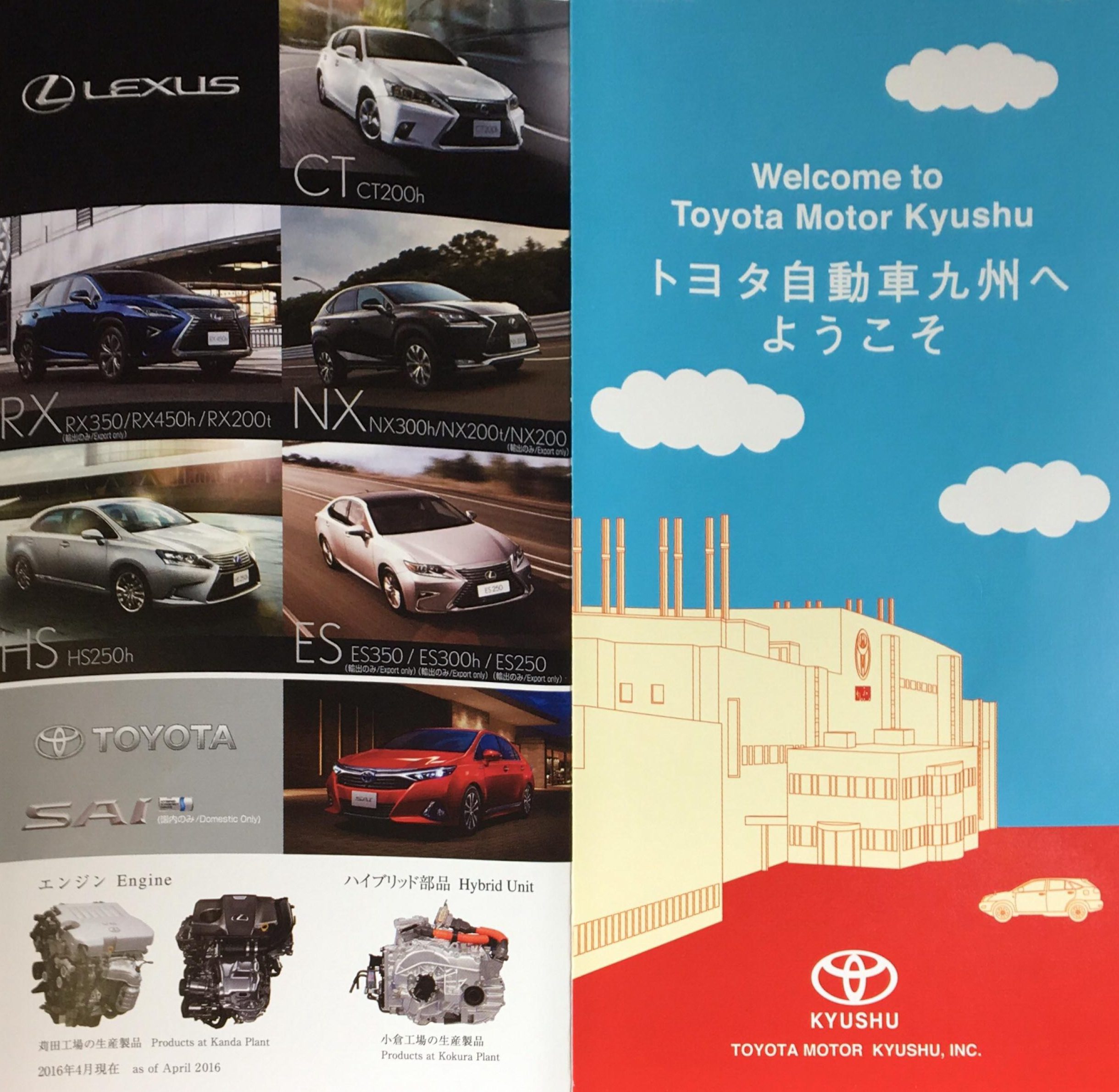
Broschüre 2
Angefangen bei der Montagelogistik zeigt sich, dass keine Gabelstapler in die Montage und innerhalb der Montage fahren. Dies dient dem Vermeiden der Verschmutzung von außen. Routenzüge und fahrerlose Transportsysteme stellen weitestgehend vorkommissioniertes Material an der Linie bereit (ca. 30.000 Komponenten pro Auto, ca. 90 mögliche Spiegelvarianten). Dabei ist bemerkenswert, dass auch viele Vormontage-Tätigkeiten von den Logistik-Mitarbeitern der Bandmontage vorgelagert durchgeführt werden.
Die Montagestationen sind flexibel gestaltet, sodass die Montagereihenfolge, wie auch der Arbeitsinhalt pro Station verändert werden kann, was eine Voraussetzung für den stationsbezogenen Kaizen (Verbesserungsprozess) ist.
Wie bei Toyota erwartet, stecken die pfiffigen Lösungen im Detail. Zum Beispiel werden alle KLT (Kleinladungsträger) nur mit durchsichtigen Deckeln abgeschlossen, sodass der Mitarbeiter stets visuell über den Inhalt Bescheid weiß.
Zur Montage:
- Schrauben angebracht an der Stoßstange mit Tüten und Klebestreifen (vorkommissioniert)
- Handhabungsgeräte, welche in Schienen geführt sind und flexibel auf die Stationen verteilt werden können
Zum Produktionssystem:
- Andon-Board an der Linie und über alle Linien
- Unterstützung durch Hanchos an der Linie mittels Rufknopf direkt am Montagewagen
- Automatisierung nur dann wenn die Arbeit (Ergonomie) für den Menschen zu anstrengend ist (Reifenmontage)
- Niedrige Bestände an der Linie und alle Teile sind vorkommissioniert und in Sequenz
- Stop-Kreuzungen: Mitarbeiter und Routenzüge stoppen und schauen (und zeigen aktiv mit dem Finger) nach rechts, links, oben, unten und überqueren erst dann den Kreuzungsbereich
- Geradeausläuferquote von 99,5%
- Verbesserung sind schnell umsetzbar, weil die Linieninfrastruktur einfach und flexibel gestaltet ist.
- Zuführungen aus Kunststoff oder Schaumstoff
Der Besuch bei Toyota war zum Abschluss der Reise noch ein weiteres Highlight. Als nächstes steht die Diskussion mit einer ehemaligen Toyota-Führungskraft an.
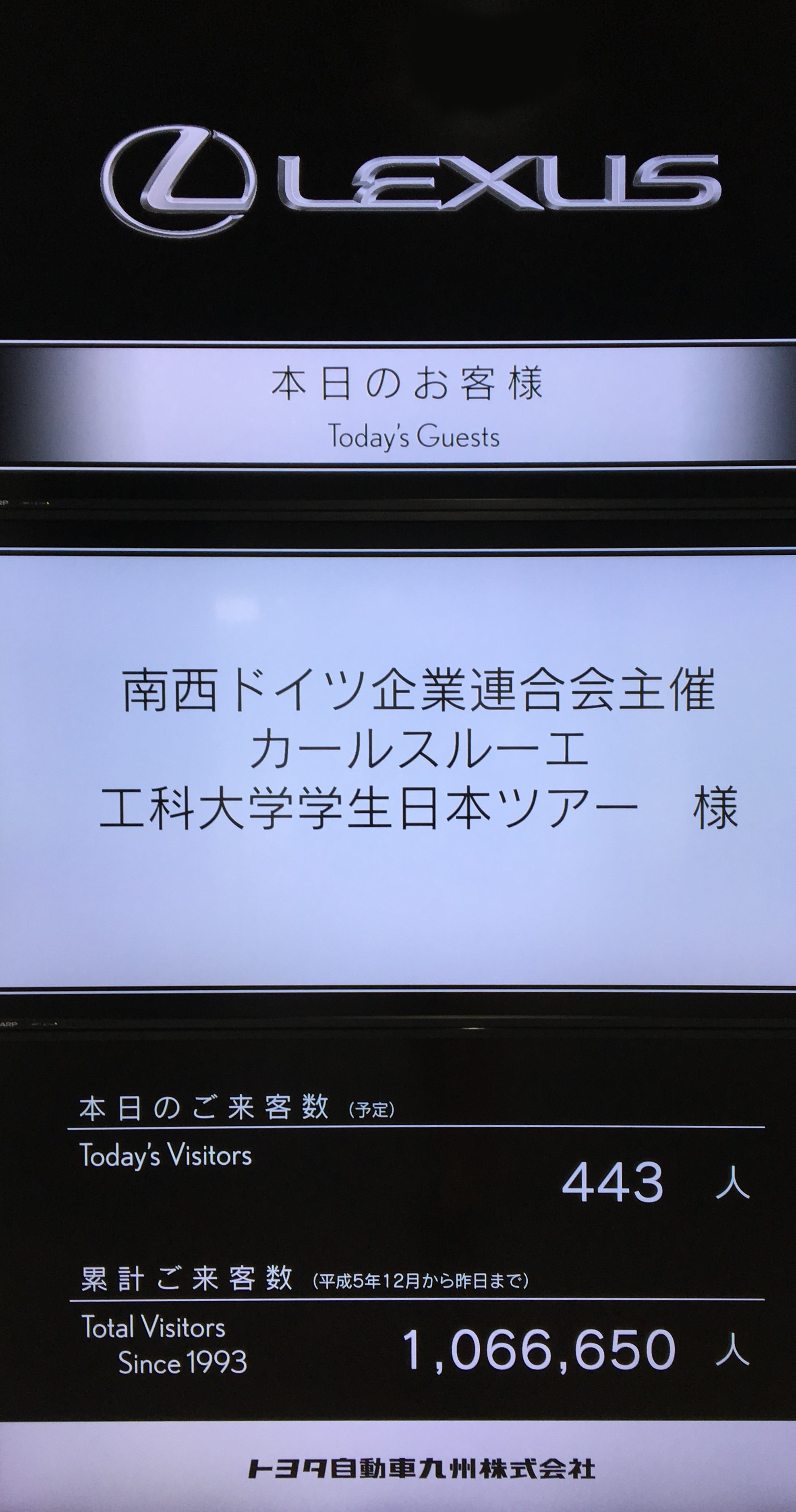
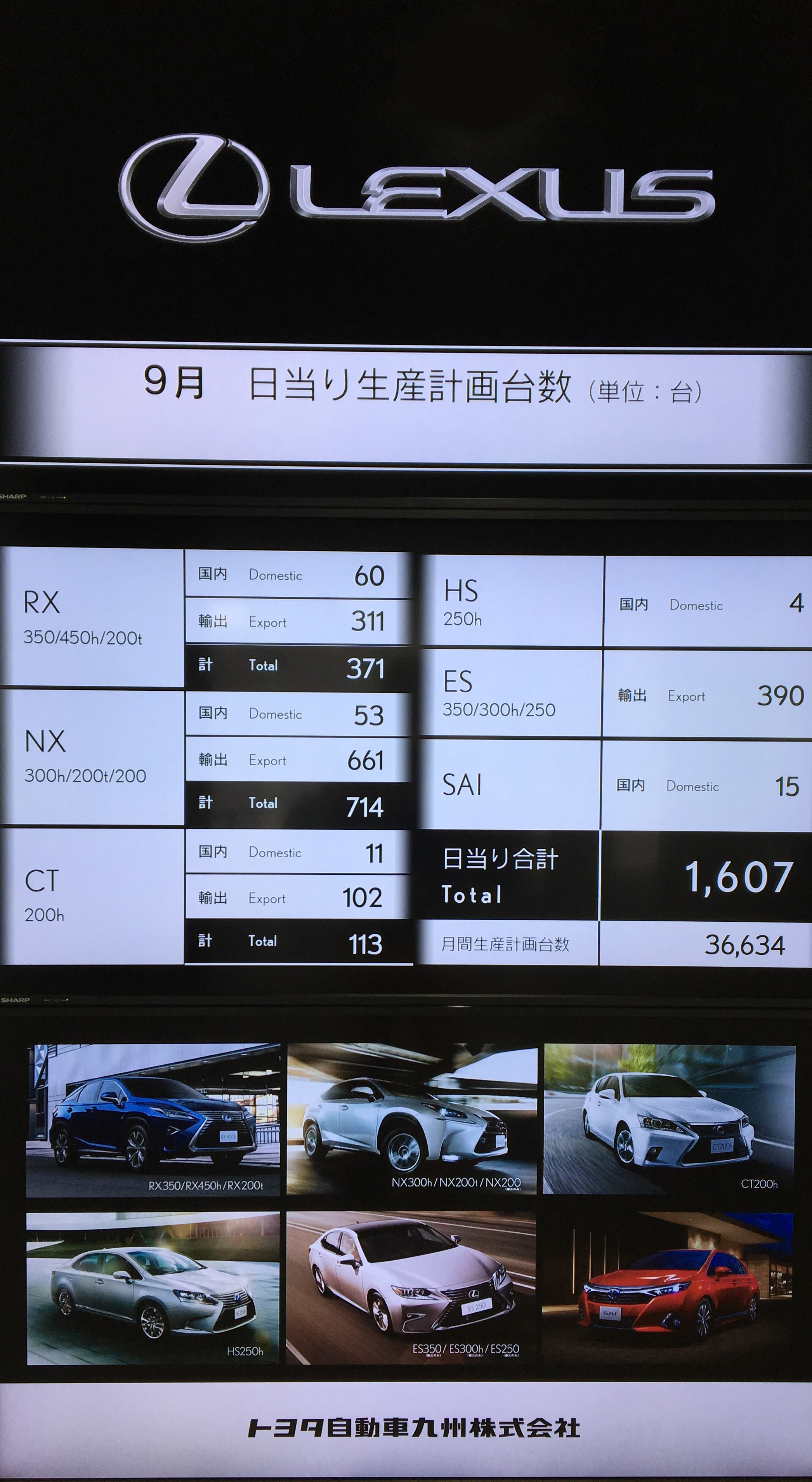